Solar Cables
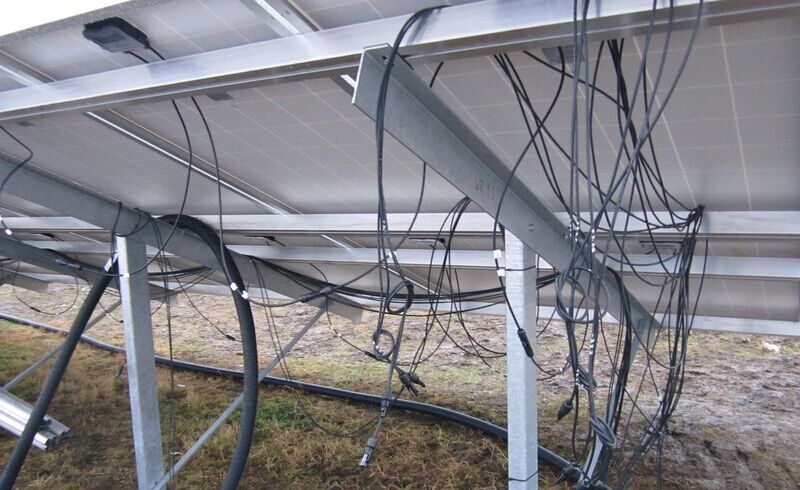
Technology advancements and changing trends in cables to meet solar PV projects requirement of a high-quality cabling system
Solar photovoltaic (PV) projects require a high-quality cabling system that connects all the electrical components together with a minimum loss of energy. A significant surge in solar PV installations during past few years in India has been responsible for driving the market for solar cables in the country. Going forward, as per industry standard, a 1 MW solar project uses around 50 km of solar cable. Given the Indian government’s target of 100 GW of installed solar energy capacity by 2022, the solar cable requirement for India alone is in excess of 5 million km.
However, being subjected to direct sun radiations and withstanding both extreme temperatures and air humidity due to cable installation usually being outdoors. These solar cables have to be sturdy and should be weather resistant. In addition, they also have to withstand mechanical stress from pressure, bending or stretching as experienced during installations as well as chemical stress in the form of acids, alkaline solutions, and salt water.
DC & AC CABLING:
DC and AC cables are an important part of Solar PV rooftop system, used in the solar power plant for generating solar energy for home/industrial/commercial rooftop or ground mounted. The 25 years life of Solar PV rooftop system can be expected only when the cables used in the solar power plant for generating solar energy for home/industrial/commercial rooftop or ground mounted are of appropriate size and quality. While solar PV panels and inverters (including junction boxes) are connected through direct current (DC) cabling, on the other hand, a connection between the inverter and the substation requires an alternate current (AC) cabling. There are three main types of DC cables and wires which are used in PV installations, namely earth wires, single core wires and twin core wires. Meanwhile, systems with single-phase inverters require the use of three-core AC cables and systems with three-phase inverters require the use of five-core AC cables.
Voltage, Size & Quality
To reduce the installation cost and increase their profit margin, many of the installers use very bad quality of cables. Even some of them do not size the cables correctly. The money saved by wrong sizing of cables and using low-quality cables is not much, but the effect of doing this to the Solar PV system is adverse. If bad quality cables are used in the solar power plant for generating solar energy for home/industrial/commercial rooftop or ground mounted, then there may be a possibility of breakage of outer insulation cover. This will reduce the system performance and make system inefficient. Cable sizing should also take into account the ambient temperature on the roof. And the cable copper conductor size should be adjusted accordingly.
For a typical solar PV project, low-voltage, medium-voltage, high voltage as well as extra high voltage power cables are used as per requirement. While low-voltage power cables are used from the panel to the combiner box, from the combiner box to the inverter, and from the inverter to the transformer, on the other hand, medium-voltage power cables are used for transferring electricity from the transformer to the substation and high voltage and extra high voltage ones from the substation to the grid.
The size of a solar cable is directly dependent on the generating capacity of the solar module as well as the distance of the solar module from the load. Hence, the larger the capacity of the solar module or greater the distance, the bigger should be the cable size. The type of components to be connected also influences the cable size. Choosing an optimum cable size helps avoid overheating and ensures very little energy loss.
Material Trends
Copper and aluminium are two most common conductor materials used in solar installations. Though copper is more expensive than aluminium, its current carrying capacity is better than an aluminium wire of the same size. In addition, the solar power cable can be solid or stranded – since current tends to flow on the outside of the wire, stranded wires have slightly better. Thus this type of arrangement is recommended for projects of larger sizes.
Subjected to harsh outdoor conditions, the wire of a solar cable needs strong insulation for protection from heat, moisture, ultraviolet light, and chemicals. Primarily neoprene for insulation was typically used by solar PV installers. However, as these neoprene-insulated cables were susceptible to cracks and damages in harsh environments. Currently, insulation made from electron-beam, cross-linked polymers is gaining traction as they do not melt or flow even at extreme temperatures.
Design Innovations
Subjected to extreme environments the solar cable industry has witnessed several innovations. One of such innovation is the development of pre-connectorized cable solutions for solar power systems to save time and ensure reliability. These solutions are ideal for utility-scale generation systems as they not only enable fast and easy connections but also simplifying installation. Similarly, DC feeder cables for connecting combiner boxes to inverters are now offered as all-in-one metal-clad cables that increase reliability and eliminate the need to install a conduit. In addition, PV cables are now also being engineered in a full array of colors to easily identify source, output and inverter circuits without the need for a time-consuming marking tape or tagging cables.
Way forward:
Manufacturers are faced with challenge of balancing costs with long-term reliability along with looking into constant innovations in product line to match with the evolving installation practices. In addition, it has been observed the codes and standards for solar cables fail to keep pace with new technologies and applications. Thus, a significant investment in R&D activities is needed to ensure the long-term performance and reliability. A significant amount of work goes into the complex process of designing and planning a solar PV power plant, whether it is on the rooftop of a building or ground mounted on the field.
Therefore, ensuring best quality standards is a must for the system, which has a life of over 25 years. Although cables constitute a small share in the total project cost, they perform crucial functions to ensure high efficiency and system longevity. Going forward, a collaborative approach involving all the stakeholders in the value chain, including cable manufacturers, standards bodies, utilities, regulators and project developers, is imperative for the sustainable growth of the solar cables industry.