Steam Turbine Solutions for Renewable Energy sectors
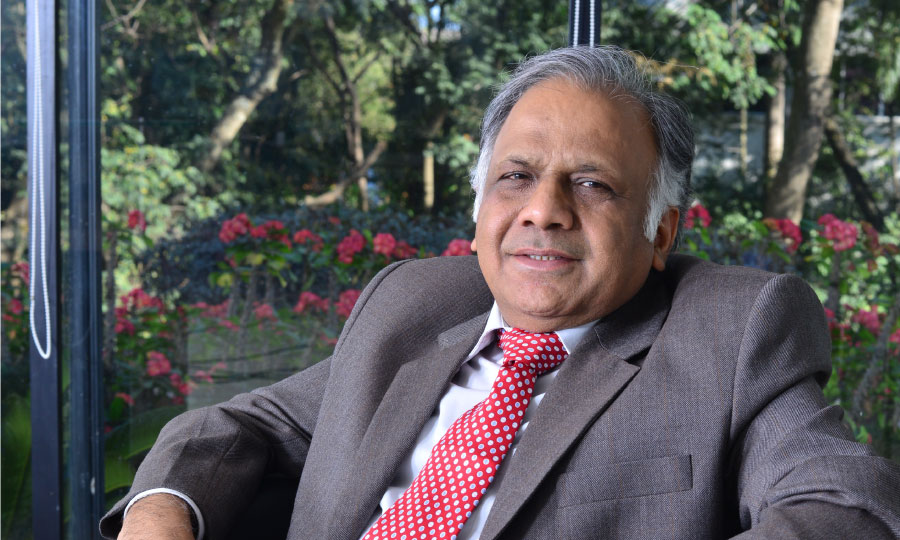
The column is authored by Arun Mote, Executive Director & CEO, Triveni Turbines. He shared his views on Steam Turbine Solutions amidst changing scenarios in the global power generation industry due to an increased focus on renewables in the energy mix.
In recent years, the global Power Generation industry has been transforming due to the changing energy generation mix and shift from conventional sources to renewable sources.
Outlook of India’s Power and Renewable Energy Sector
India’s need for energy is increasing rapidly, owing to economic growth. Rapid industrialization and urbanization over the past few years have led to an increase in energy demand. According to the latest Government statistics, in FY20, the gross electricity consumption has gone up to 1,208 kWh per capita and the peak electricity demand to 183 GW.
As of March 2021, India’s total installed power generation capacity is 379 GW. This includes 91 GW of capacity from renewable energy sources. Of this, 10 GW capacity is from Biomass power (Bagasse and Non-Bagasse), followed by 147.6 MW from Waste to Energy, according to the Ministry of New and Renewable Energy (MNRE).
According to the 19th Electric Power Survey conducted by the CEA, the all-India installed power generation capacity is projected to grow to 619 GW by the end of 2027, of which India aims to have 275 GW from Renewable Energy Sources.
Renewable Energy Industry
Globally, there is an increasing focus on the replacement of existing coal-fired power plants with clean fuel generation in order to reduce carbon footprint. This will further augment the demand for renewable power generation in the future.
Renewables comprise of non-thermal (such as Hydro, Solar and Wind) and thermal energy sources (such as Biomass, Waste Heat, and Waste to Energy). Independent Power Producers (IPPs) play a major role in generating power for sale to the grid or to specific customers. Captive power producers generate electricity to meet their own power demand, lessen the cost of power generation, and to transmit the surplus power to the grid.
Captive power generation units can be fired using fossil fuel and renewable fuel. The largest market for captive power generation in the country is the Industrial sector, mainly on account of the increasing demand for electricity from energy-intensive industries such as Cement, Iron & Steel, Petroleum Refineries and Chemicals, etc.
The Combined Heat and Power (CHP) systems or co-generation system generates electricity or mechanical power with lower emissions compared to conventional power generation systems (fired using fossil fuels). Thus, CHP /co-generation is widely preferred for captive power generation using thermal renewable energy sources such as Bioenergy, Waste Heat, Residual Waste, Solar Thermal, and Geothermal, for power generation, heating, and cooling applications.
Thermal Renewable Energy Industry
Bioenergy will remain the predominant source of thermal renewable energy. Its share is expected to decline due to the expansion of alternate renewable power generation technologies, namely Solar, Photovoltaic and Wind. Higher acceptance of Bioenergy will increase investment in Biomass-based power plants globally.
The Bioenergy potential in India has been estimated at 25 GW in 2022, and the Government of India (GoI) has been consistently promoting the Biomass Power and Bagasse Co-generation programme. According to MNRE, the total installed capacity is 10 GW from Biomass Power and Bagasse Co-generation Sector as of March 2021.
India’s current bagasse-based co-generation target from the Sugar industry in 2022 is 10 GW and by 2027 is 16 GW, according to MNRE estimates. This target is possible if there isa significant increase of sugarcane crushing capacity, favorable weather conditions and increased yields of sugarcane, leading to higher utilization of bagasse-based co-generation target in the future.
Steam turbine solutions for the Thermal Renewable sector
With a sustained focus on adopting innovative technology, backed by seamless execution; leading domestic steam turbine manufacturers have emerged as a trusted service provider to clients around the world. This has been done by consistently strengthen their position in the Industrial sector by meeting the captive and independent power requirements of their customers in various Greenfield and Brownfield projects.
Thus the domestic players have been able to drive the market growth by establishing a stronger global footprint and offering a wide range of state-of-the-art steam turbines, coupled with an excellent aftermarket portfolio to meet the needs of its customers round the clock.
Biomass (bagasse and non-bagasse) as fuel helps the CHP/cogeneration system to generate power that is sustainable. Industrial use of bagasse-based co-generation, particularly from sugar and palm oil mills, is conducive to the production of power from biomass. The Pulp and Paper industry constantly focuses on improving energy efficiency, which is attained through increased use of non-bagasse (e.g. wood waste) based power generation, and by efficient usage of steam.
Typical Biomass power plant configuration
The rapid depletion of fossil fuel reserves and the environmental impact of CO2 emissions have brought sustainable energy solutions to the forefront. The drive to utilize locally available biomass and the benefit of generating power closer to the point of consumption has enabled the setting-up of biomass-based Independent Power Plants (IPP).
The waste heat recovered from other industrial sources/processes is commonly found to generate steam and electricity in Cement processing, Iron and Steel processing, Petroleum Refining and Chemical processing, etc. The heat from the hot steam is recovered using Heat Recovery Steam Generators (HRSG) or Waste Heat Recovery Boiler (WHRB) for the generation of superheated steam that can be used in process heating (co-generation) or to drive a steam turbine (combined cycle).
Thus, the inclusion of a CHP/cogeneration system by the utilization of hot exhaust gas from the production lines is to reduce the operating cost.
For example: – Waste heat recovery (WHR) based power plant installed in cement plants, uses the heat generated through rotary kiln preheater (PH) and after quenching cooler (AQC) exhaust hot gases for power generation.
Despite the fact that incurs a high initial cost of investment, the concept of WHR is slowly picking up across the country. To conclude, a rapid increase in electricity consumption, along with a growing focus on electricity generation through thermal renewable energy sources, is expected to unleash sustainable power generation in the country.
Case Studies on Triveni Turbines
-
Bagasse based Cogeneration plant installed overseas
Driven by 30 MWeback pressure steam turbine with an inlet steam of 65 Bar and inlet temperature of 500 Deg C with 2.5 Bar Exhaust.
Challenge
- Customer’s requirement for higher efficiency steam turbine and the delivery expectation was 7 months
Solution
- A steam turbine with reaction technology to meet the customer’s requirement
- The steam path is designed to handle very large volumetric steam flow and the rotor with Reaction blading provides higher efficiency
- Modernized facility along with strong global sourcing network led to meeting the delivery challenge in record time
Benefits
Single cast exterior casing with Guide blade carriers for faster startups and reaction stages offer better efficiency
With rising costs, operating turbines efficiently is a necessity for cost-saving and creating a positive carbon footprint. With changes in the requirement of the process or age, the turbines become inefficient and impact costs. Once the customer’s current needs are understood, the turbine may need to be re-designed to meet the new parameters and is running efficiently, leading to cost-saving.
There are times when the price of power spirals down, leading to a loss for power producers. In the case of process industries like sugar cogeneration plants, where part of the revenue comes from exporting power, the cost of the power will drag down the profitability of the company.
This situation is addressed by optimizing the customer’s existing turbines to suit the market demand.
For Example:- A sugar cogeneration customer operating a European / Chinese make, extraction condensing Turbine.
When the cost of power turns unattractive, the customer will have to forcefully run the turbine at a higher flow as the steam is required to cater to the process in addition to the minimum flow being sent to the LP section of the turbine. Without this minimum flow, the blades in the LP section get heated up and will melt leading to huge damage to the rotor. Though this flow generates additional power, this will not benefit the customer as the price of power could be lesser than the cost of producing. In addition, the turbine would be operating inefficiently i.e., higher specific steam consumption as it would run in part-load condition.
How can the customer avoid the dual loss of avoiding producing additional steam to the condenser and operating the turbine efficiently?
Solution:
This single extraction condensing turbine will be converted to a backpressure turbine with a modular design.
Benefits:
The engineers study the process change requirements of the customer and redesign the existing turbine by modifying the steam flow path to the new parameters. This re-engineering process is carefully done to ensure the existing system (i.e., casing, civil foundation, lube oil system etc) is retained. The only modification will be the turbine internals (i.e., new rotor, diaphragms, and bearings subject to design requirement) to suit the upgraded blade path.
The re-engineering will be done to ensure the old rotor and stator can be reused within the existing casing once the price of power improves, thereby giving the customer flexibility of choosing any option based on the fluctuation of power pricing and enhancing the efficiency in either case scenarios.
Benefits of Efficiency improvement
- Up to15% improvement in efficiency
- ROI under 2 years
- Upgraded Steam flow path design
- Retain the civil foundation
- Existing Turbine housing
- Life extension by over 100,000 hours
- Increase in the span between 2 overhauls
- Reduced carbon emissions
A process cogeneration plant operating their 8MW European OEM Turbine for more than 15 years.
Challenge:
Due to changes in power requirement, they were operating the turbine inefficiently. We reviewed the turbine and confirmed to the customer we would modify the parameters as per the current requirement and also ensure the availability of 1 MW additional power.
Solution:
To route the additional steam to the existing Turbine with upgraded steam flow path design.
Benefits:
By modifying the Turbine internals (Rotor with high efficient blades, Diaphragms, Bearings, and Gear Internals) with the new design the customer could achieve a power enhancement of 9 MW with lower Specific Steam Consumption than the normal running condition.
The overall project cost was significantly lower as there was no modification to the civil foundation and also the Turbine housing was retained. The turbine was commissioned and handed over with a 1 MW power addition and process stabilization, the payback is achieved in less than a year.